Vacuum system CC
Single-grade plastic processing for pelletizing processes
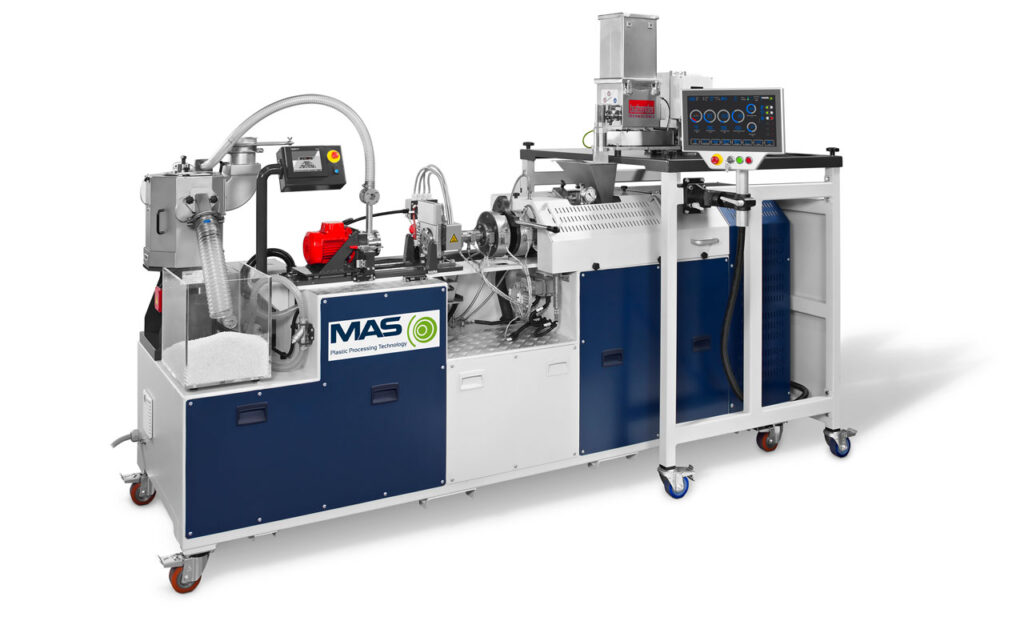
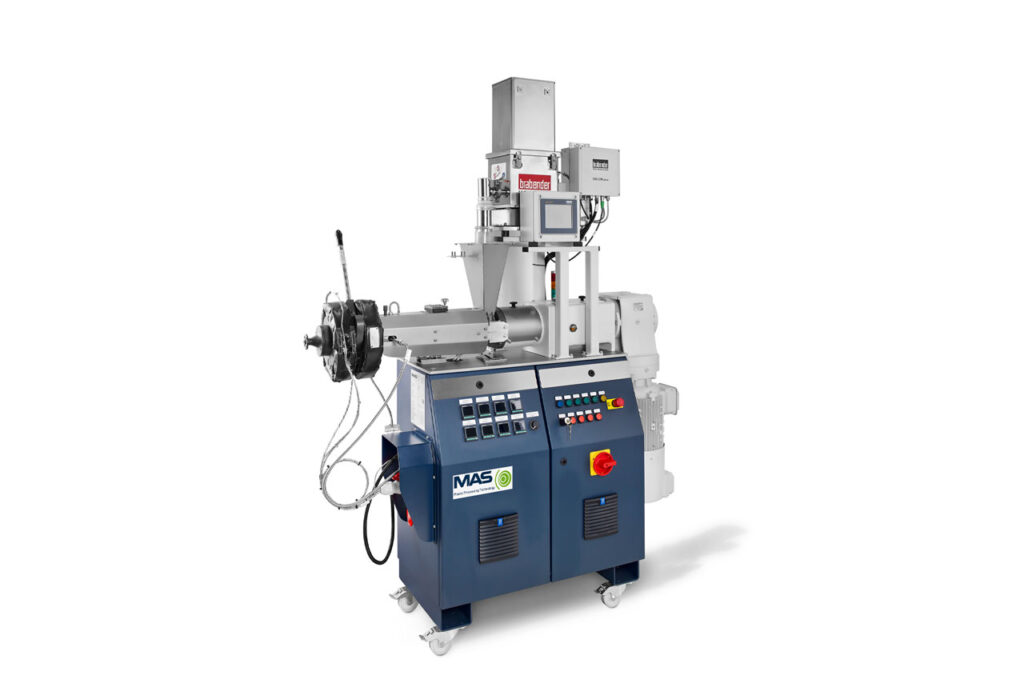
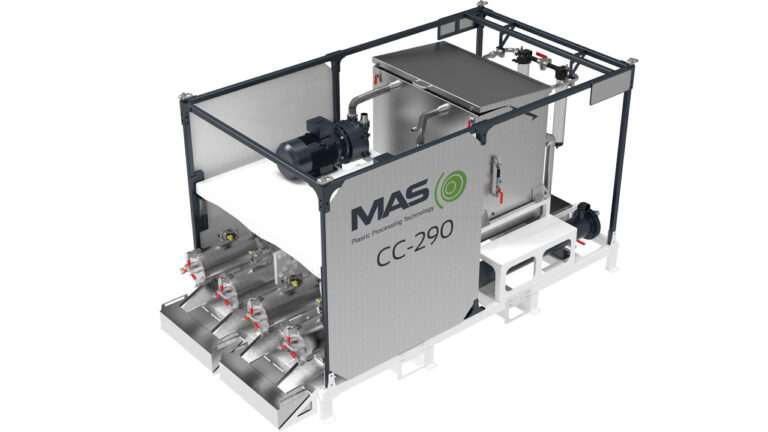
Sophisticated process water system solutions provide water ring vacuum pumps with a targeted and reliable supply of water. An included system for the treatment of process water reduces the consumption of fresh water, works sustainably and conserves resources.
MAS 110
Powerful.
Innovative.
Big & Compact.
The new MAS 110 extruder increases throughput and productivity when recycling and upcycling plastics — ideal for larger recycling and compounding plants.
Convincing advantages
Perfect for test runs
low material input and realistic production conditions — ideal for material sampling and recipe development
High performance
Quality comparable to large MAS extruders with significantly lower throughput (15–30 kg)
Simple maintenance
Fast and effective, without system downtime
Cost savings
thanks to low material input and low additive inflow, can be used primarily in the test environment
How the vent extruder TA works
The extruders for verting are used for materials that require degassing at the end of the melting process—after the twin screw and the melt filter. The melt flow is divided into numerous smaller partial flows by the melt distribution block in the entry area of the extruder’s specially developed venting screw. This increase in surface area enables particularly efficient extraction of the melt via the three venting openings, using a vacuum system. This removes liquid, air, and impurities in a precise manner. The optimized melt flow can then be fed into further processing in the best quality.
After venting in the extruder, the single-screw extruder builds up the melt pressure necessary for the downstream pelletizing process. This relieves the pressure on the upstream extrusion and filtration processes and significantly increases the throughput and efficiency of the entire extrusion line. The result: the highest quality at all pellet levels for all conventional plastics.
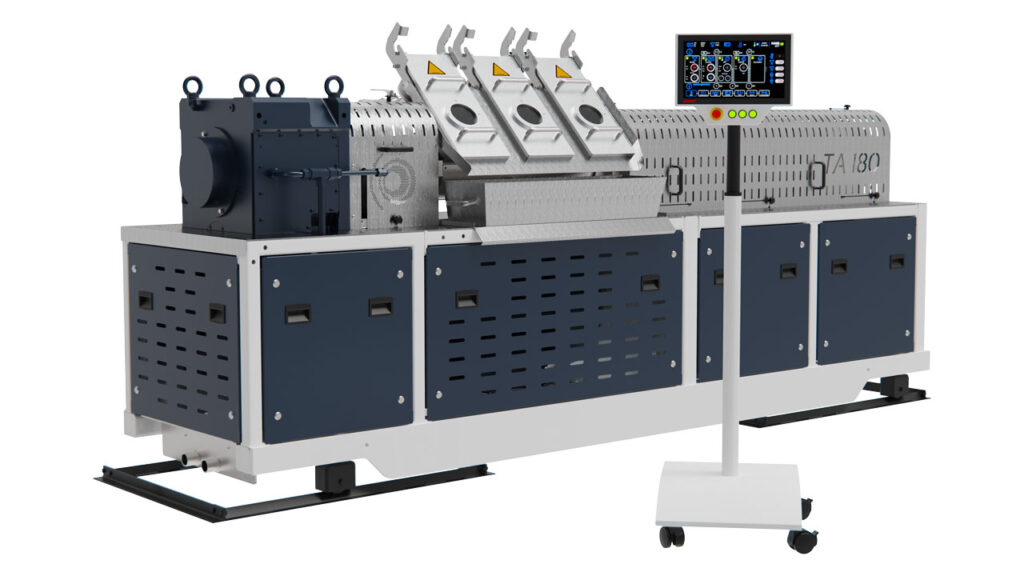
Vent extruder TA in three versions
To guarantee the best possible quality for individual requirements, our vent extruders are available in several versions: TA 100, TA 140, and TA 180. The number stands for the diameter of the extrusion screw (in millimeters). The venting performance is correspondingly higher or lower with the corresponding material input, as are the heating and drive power. Modifications in the area of venting and pressure build-up are available on request.
Due to their high performance and efficiency-boosting processing, vent extruders are often integrated into large extrusion lines and are part of the MAS upgrade line, which is used to improve the quality of the granulate. All options for vented screw extrusion guarantee the pure processing of HDPE, LDPE, PP, and PS, as well as various special plastics (tested on request in a material-conserving laboratory environment). The result: better performance and better quality along the entire extrusion line.
Energy savings
calculate
Interactively calculate the achievable energy savings compared to classic extrusion solutions and discover that our upcycling technologies not only improve quality but also reduce the payback period of your investment. Enter your energy and consumption data into the energy calculator and see the difference!
Energy price per KwH (EUR) |
Output Kg/H |
Working Hour Per Year |
|
Input |
Extruder |
Energy Cons. KwH/KG |
Energy price per KwH (EUR) |
Output Kg/H |
Working Hour Per Year |
Output Kg/Year |
Total Energy Cosumption KwH |
Total Costs for Electrical Energy |
MAS — extruder |
|||||||
single screw ecxtruder |
KWH |
€ EURO |
|
Energy Saving/Year |
||
Cost Saving / Year |
Further benefits of our unique technology
better pellets thanks to large degassing surface
through targeted, high-precision degassing
seamless feeding, venting, and processing within the extrusion line without waiting times
targeted pressure build-up for downstream granulating and processing steps
for various industries, with optional tests in the MAS Technical Center
can be installed in existing plants and as part of the upgrade line
low wear and easy maintenance
venting and pressure build-up area can be adapted on request
Securing laboratory extruders for
material development
In the test environment and during recipe development, the MAS 24 and MAS 55 laboratory extruders deliver fast results under realistic production conditions without high material costs. Are you looking for a laboratory extruder for your development area? We can advise you on complete planning, design and commissioning in the testing and R&D environment. We look forward to receiving your inquiry!

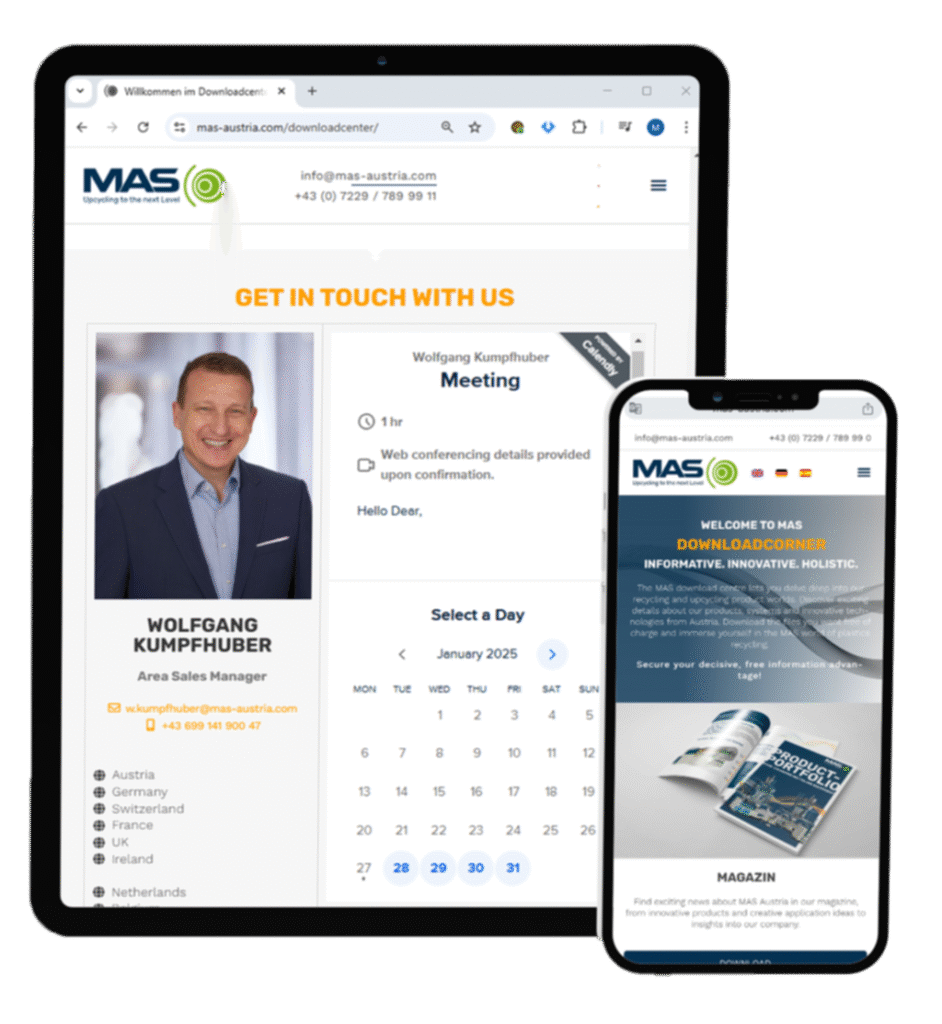
DAS SAGEN UNSERE KUNDEN
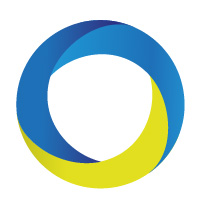
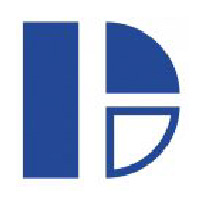
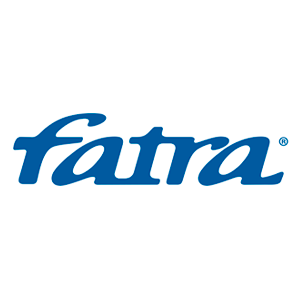

Secure extruder with
added value
Are you looking for a twin-screw extruder for your company? Our extrusion experts can advise you on everything from planning and designing completely new extrusion lines to upgrading or retrofitting existing lines. We look forward to receiving your inquiry!
ABOUT MAS
Founded in 2006 by recycling pioneer Helmuth Schulz, the company is revolutionizing the extremely high quality standards of twin-screw extruders for the recycling industry. Thanks to patented technology, MAS meets the challenges of modern recycling and upcycling requirements and has developed into an international innovation driver within a very short space of time. The environmentally friendly added value with simultaneous energy and resource savings is therefore used worldwide.
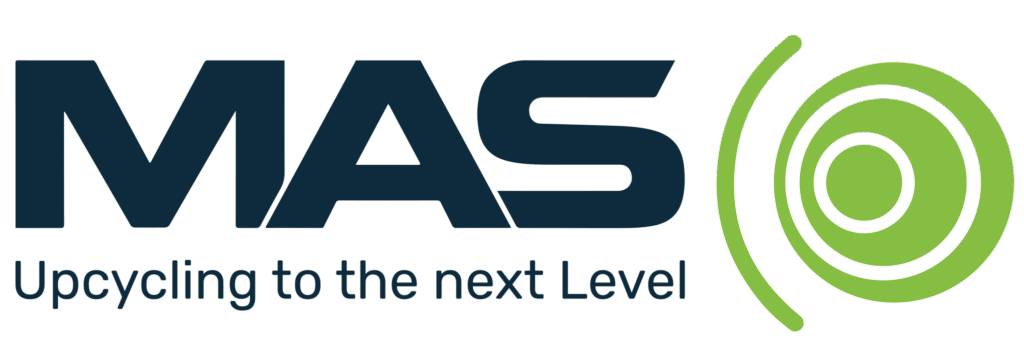
Contact us
- Austria
- Germany
- Switzerland
- France
- UK
- Ireland
- Netherlands
- Belgium
- Luxembourg
- Sweden
- Norway
- Finland
- Poland
- Italy
- Spain
- Portugal
- Lithuania
- Estonia
- Latvia
- Mexico
- Brasil
- Slowakia
- Slovenia
- Croatia
- Romania
- Hungary
- Czech Republic
- Turkey
- Japan
- China
- South Korea
- Vietnam
- Indonesia
- Thailand
- Israel
- Australia
- USA
- Canada